Client Overview
National Retailer Operating Extensive Network of Distribution Centers
Our client faced mounting pressure to optimize storage and retrieval processes. Their primary cold storage facility served as a critical hub for temperature-sensitive goods, but increasing inventory volumes were straining the existing infrastructure.
Business Challenge
Several Obstacles in Warehouse Operations
Capacity Constraints: Traditional racking systems were insufficient to meet growing demands, leading to the need for third-party storage services.
High Labor Costs: Manual stocking and retrieval processes were resource-intensive and prone to delays.
Limited Space Optimization: Expanding the facility horizontally was not an option, making vertical storage the primary focus.
Solution
Deployment of a New AS/RS System
To overcome these challenges, the client deployed a scalable Automated Storage and Retrieval System (AS/RS). The solution featured cutting-edge vertical storage technology and automated let-downs.
Vertical Expansion Using AS/RS
- Utilized high-capacity cranes to store pallets vertically, effectively doubling the storage capacity within the existing space.
- Optimized the layout to maximize density without compromising retrieval efficiency.
Automated Inventory Management
- Implemented crane-based retrieval that replaced manual stocking methods, reducing errors and labor-intensive tasks.
- Real-time monitoring and automated replenishment streamlined inventory control.
Integrated Temperature Control Optimization
- Designed airflow and temperature regulation systems that maintained ideal storage conditions for perishable goods while supporting increased pallet loads.
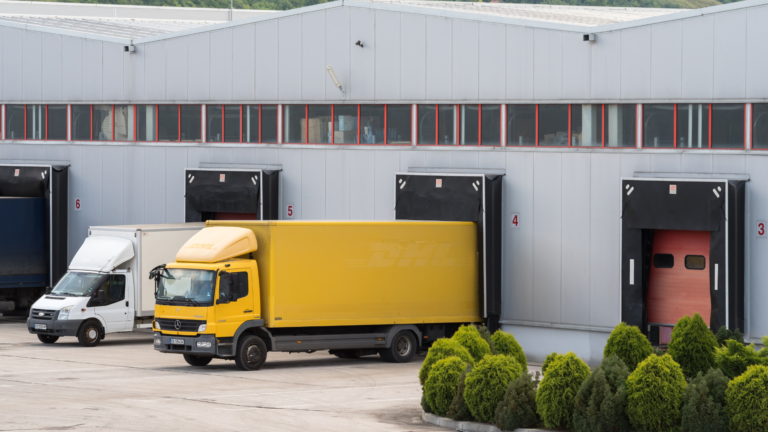
Result
Goals Achieved, Workflow Improved, and Costs Reduced
50% Increase in Storage Capacity: Achieved without expanding the warehouse footprint.
35% Reduction in Labor Costs: Automation reduced dependency on manual labor while improving accuracy.
Improved Throughput: Faster stocking and retrieval processes enhanced operational efficiency and reduced delays.
Scalability and Future Enhancements
The system was designed to scale alongside the client’s growth plans. Potential future upgrades include:
Predictive Analytics Integration: Utilize AI to forecast inventory peaks and further optimize storage allocation.
Dynamic Cost Allocation: Implement activity-based costing to measure storage efficiency and adjust for fluctuating demand.
By embracing advanced automation, the client transformed their warehouse operations, resulting in significant cost savings and productivity gains. This case highlights the power of scalable technology for organizations seeking to optimize logistics and reduce operational expenses.
For businesses interested in similar solutions, contact us to explore tailored automation strategies that fit your needs.