Warehousing
Transforming Warehouse Operations with Automated Billing and Activity-Based Costing
Client Overview
High-Volume
Warehouse Operation
The client faced significant challenges in managing billing and invoicing processes for a dynamic workforce and equipment-intensive environment. With fluctuating demand, seasonal peaks, and a mix of permanent and temporary staff, the client sought a solution to improve billing accuracy, optimize cost allocation, and ensure compliance with labor and safety regulations.
Challenge
Several Challenges In Place
Dynamic Workforce Management:
The warehouse relied heavily on temporary staff alongside permanent employees. Tracking hours, roles, and activities across shifts manually led to frequent errors and inefficiencies in the billing process.
Equipment Usage Monitoring:
The operation involved numerous machines, each with unique maintenance, depreciation, and utilization costs. Manual allocation of equipment-related expenses to specific tasks or shifts was error-prone and time-consuming.
Demand Fluctuations:
Seasonal peaks and troughs in operational output created variability, making it challenging to align labor and equipment costs with revenue.
Compliance and Reporting:
Adhering to labor laws, safety standards, and operational regulations required extensive documentation and manual reporting, increasing administrative overhead.
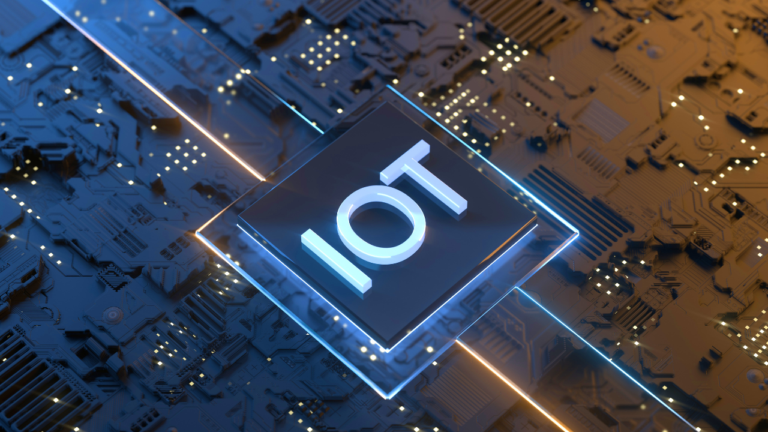
Solution
Implementation of New Billing and Costing System
To address these challenges, the client implemented an IoT-enabled billing and activity-based costing system designed to streamline processes and improve operational efficiency. The solution included the following components:
IoT Integration for Real-Time Data Collection
- IoT sensors were deployed across the warehouse to monitor equipment usage, task completions, and workforce activity.
- Real-time data was aggregated into a centralized system, providing granular insights into performance metrics for each shift and resource utilization.
Role and Activity-Based Cost Allocation
- An intelligent system processed IoT data to dynamically allocate costs based on roles, shift activities, and equipment usage.
- Activity-based costing models ensured that every operational expense was mapped directly to specific tasks or outputs, improving billing precision.
Predictive Maintenance and Resource Prioritization
- Predictive analytics identified potential equipment failures, enabling proactive maintenance to reduce downtime.
- Staffing and resource allocation algorithms were optimized for peak demand periods, ensuring operational efficiency without incurring excessive costs.
Automated Compliance Reporting
- Detailed compliance reports were generated automatically, ensuring adherence to labor laws and safety standards.
- Comprehensive audit trails were maintained, reducing the manual effort required for regulatory reporting.
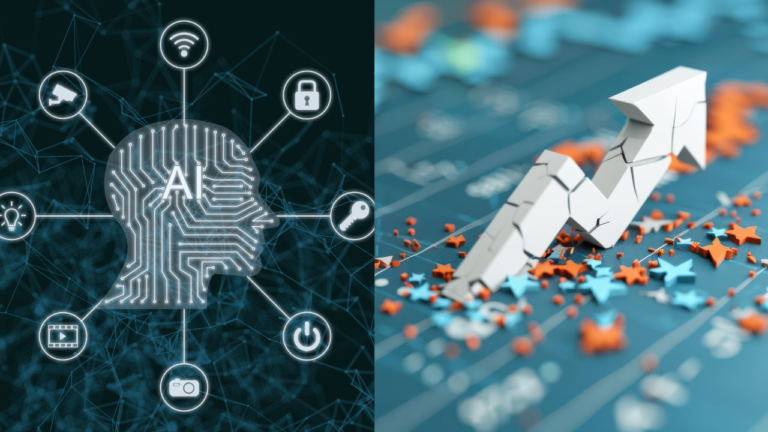
Result
Seamless Integration with Existing Systems
AI-Driven Demand Forecasting:
Leveraging machine learning to predict seasonal peaks and proactively adjust staffing and resource allocations.
Blockchain Integration:
Ensuring secure, transparent invoicing and payment tracking for all stakeholders.
Advanced Analytics:
Utilizing operational data to drive continuous process improvements and identify further cost-saving opportunities.